What is welding?
Joining things together (joining) is done in many aspects of manufacturing. Junctions are broadly classified into three categories.
1Mechanical joining method
(fastening with bolt nuts, riveting, etc.)
2Metallurgical bonding (welding)
3Chemical bonding methods (e.g. adhesive)
Among them, welding refers to the metallurgical joining method.
Type of welding
Welding is further classified into the following three types.
A method of melting the metal contact parts to be joined using heat such as gas flames and arcs to fuse and bond the atoms of both.
Arc welding and laser welding fall into this joining method.
2Pressure welding (resistance welding)
A method of joining heated joints by applying pressure.
3Brazing process
How to glue between the metals to be joined.
We develop and manufacture welding equipment for fusion welding (arc welding) and pressure welding (resistance welding).
Of course, there are some examples of using our robots in brazing methods depending on the combination of applications. Contact us for more information.
Of course, there are some examples of using our robots in brazing methods depending on the combination of applications. Contact us for more information.
What is an arc?
An arc is a discharge phenomenon that emits light at high temperatures. When a contact or energized electrode is separated, an arc is generated between the electrodes.
The temperature of the arcs, for example for TIG welds, will reach a center temperature of approximately 16,000°C.
(This is a temperature that is higher than the sun's surface temperature by approximately 6000°C and significantly exceeds the metal's melting point.)
It may seem that there is no familiarity with the discharge phenomenon, but an arc phenomenon also occurs in our familiar places.
For example, the arc phenomenon is a spark that comes out when an electric appliance's outlet plug is pulled out, or a blue-white light that occasionally appears between the pantograph of an electric train running on a rainy day and the contact wire.
However, as can be seen in these examples, arcing in nature is transient and does not occur continuously.
In this way, the arc discharge phenomenon is usually unstable, but the welding machine plays the role of stabilizing the discharge to use the arc as a heat source for welding.
Classification of arc welding methods
Arc welding can be broadly divided into consumable electrode type (consumable electrode type) and non-consumable electrode type.
Arc discharge is generated between electrodes when energized electrodes are separated. In arc welding, one of these electrodes melts to form a workpiece to be joined.
In terms of what is used for the other electrode, it can be divided into a consumable electrode type (consumable electrode type) in which welding wire or the like is used to join them while melting them, and a non-consumable electrode type (non-consumable electrode type) in which a tungsten electrode is used to generate an arc between the electrode and the workpiece.
CO2 welding, MAG welding and MIG welding are classified as the melting electrode type, and TIG welding and plasmawelding are classified as the non-melting electrode type.
CO2/MAG welding
CO2 welding uses CO2 (carbon dioxide) as the shielding gas, and MAG welding uses mixed gas as the shielding gas. This method is used for ordinary steel products.
MAG is an acronym for Metal Active Gas and Active Gas is an acronym for active gases.
CO2 contained in the mixed gas diverges due to high-temperature arcing and becomes an oxidizing gas, so this name is given.
Based on this term, CO2 welding is also a type of MAG welding. However, it is common to refer to CO2 welding and MAG welding separately, so here we distinguish and explain CO2 welding and MAG welding.
Stainless steel may also be welded using stainless cored wire.
MIG welding
MIG welds are constructed using an inert gas such as Ar (argon) as a shielding gas. They are used in non-ferrous metals such as stainless steel and aluminum.
MIG is an acronym for Metal Inert Gas.
An inert gas of 100% is used in the case of aluminum, but a gas containing a small amount of active gas (such as O2) is used in the case of stainless-steel to ensure stable arcing.
TIG welding
TIG welding is an acronym for Tungsten Inert Gas and uses tungsten-electrodes to weld inert gas such as Ar (argon) as a shielding gas.
There are two methods of inserting filler metal (sometimes called "filler rod" or "filler wire"), which does not insert filler metal.
As TIG welding only melts the base metal, the welded metal from the electrode cannot be obtained unlike the welding method of the molten electrode type. The latter method is used when it is necessary to secure the welding quantity from the viewpoint of strength, etc.
There are two types of welding machines: one is dedicated to direct-current welding and the other is dedicated to alternating-current welding. Alternating current is required in the case of aluminum or magnesium welding, so it is necessary to select a welding machine for both AC and DC.
Why Shield Gas is Required
High-temperature metals during welding tend to dissolve in the atmosphere (nitrogen, oxygen, etc.), and solidify without these gases escaping during solidification, resulting in defects such as blowholes (bubbles in the interior) and pits (holes on the bead surface).
Blow holes and pits greatly affect the joint strength, so shield gas must flow to protect the molten metal from the atmosphere.
Pulse welding
This welding method outputs pulse current and base current alternately.
Pulsed MAG/MIG weld
In the electrode welding method, the electrode wire is welded while being melted.
The wire will melt and weld to the base metal. However, in a certain current range, the droplets formed at the tip of the wire will increase, leading to spatter.
When pulse welding is used, it is possible to forcibly desorption before excessive droplets are formed by high pulse current. Therefore, welding with less spatter can be easily obtained even in the current range where sputtering tends to increase in direct current.
In addition, when aluminum or stainless steel is welded by DC MIG welding, the bead tends to become acclimated to the base material due to insufficient heat input, particularly in the low current range. However, pulsed welding in such a situation makes it easier to obtain smooth bead.
Pulsed TIG welding
As it is a non-melting electrode type welding method, pulse current, base current, and pulse frequency can be arbitrarily set.
There are various usage modes. For example, when the pulse frequency is set to a low value, the base material is melted during the pulse current, and the heat input control that promotes solidification by the base current is expected to improve the allowance for attitude welding and plate thickness difference.
On the other hand, the higher the pulse frequency, the better the directivity of the arc. This is advantageous in terms of the molten pool formation rate at the welding start point because the arc concentration is improved. In addition, the arc is stabilized where the arc tends to fluctuate in low-current welding, which makes thin plate welding easier.
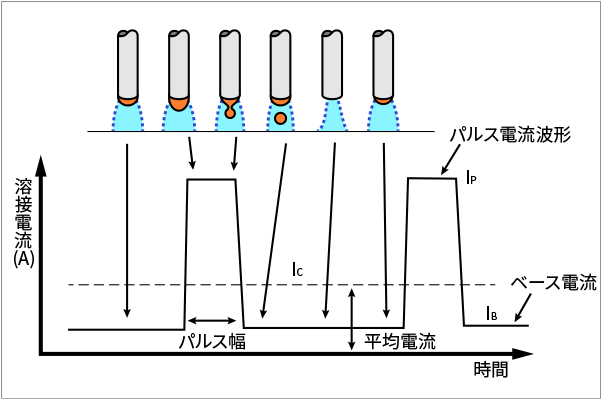
Control image of pulsed MAG welding
Why AC Welding is Required for TIG Welding of Aluminum
Oxide film is always formed on the surface of aluminum material. This oxide film has a very high melting point compared with that of aluminum. In DC TIG welding, this oxide film does not weld well in the way.
In DC TIG welds, the tungsten electrode is on the negative side, but when the electrode is on the positive side, it is known that the oxide film is broken (cleaning action).
For this reason, by creating a phase in which the tungsten-electrode becomes the positive pole periodically in AC TIG welding, the oxide film is broken and welding is enabled.
Plasma welding
Plasma welding uses a tungsten rod as an electrode, just like TIG welding. The tungsten electrode is covered with a water-cooled nozzle electrode and is welded using a thin, narrow plasma arc.
Compared to TIG welds, a thin plasma arc improves the weld rate, increases the penetration depth, realizes keyhole welding (back-wave welding with I-type butt joints), and hardly affects the weld width even if the standoff (distance between the electrode and base metal) expands.
Laser welding
Laser welding uses laser light as an energy source to melt and join metals.
What is a laser beam?
Laser light is an artificial light that does not exist in nature.
When sunlight is collected with magnifying glasses, the area becomes brighter or warmer, but natural light has a limit on its collection because its direction and phase are scattered.
On the other hand, laser light is an artificially generated light with a single wavelength and directivity, and it is possible to collect the energy by converging it to a small extent based on its characteristics.
By using the characteristics of such laser beam, it is possible to ensure high energy density enough to melt the metal, so it can be utilized for welding.
Principle of laser
The word source is the acronym for Light Amplification by Stimulated Emission of Radiation (Amplification of the beam by stimulated emission).
The atoms that make up a substance are composed of nuclei and electrons. When an atom receives energy from the outside, the electron's orbit changes (an excited state, the electron in this state is called an excited electron), but since this state is an unstable state, the excited electron tries to return to its original stable state, at which time photons are emitted.
In this particular material, light of a certain wavelength is received and becomes an excited state, and light of the same wavelength as the excitation light is emitted (stimulated emission) when returning to the original state. Such materials are used as laser media.
When the excitation light is put into the laser medium in which the resonant mirror is arranged at both ends, the light reflected by the mirror reciprocates between the mirrors, and the light emitted by the stimulated emission is amplified in a chain manner.
Laser welding takes out this amplified light and uses the energy for welding.
Expanded use of laser welding
Laser welding has an advantage over other welding methods, such as high-speed welding and penetration. However, since the laser beam is concentrated at the target position, high aiming accuracy as well as the accuracy of the jig side is required.
We offer a lineup of high-precision robots with the world's highest level of trajectory accuracy and meet the requirements for laser welding.
In addition, in combination with the wobble head, the laser beam can be diverted by the mirror built into the head to enable high-speed scanning of the focal point on the workpiece. It is also possible to use the wobble function to stabilize the process and increase the tolerance for gaps and misalignments.
In addition, we are further expanding the use of laser welding by developing a laser synchro-feed hybrid welding system that, in combination with synchro-feed welding, which is our ultra-low sputter welding method, provides a higher gap margin while taking advantage of high-speed welding, which is the strength of laser welding.
Be based on downward welding Reason
In welding, parts that you want to join are melted to make them liquid and integrated.
Imagine a glass of water poured into it. It will not spill if the cup is placed on a horizontal surface, but water will spill if the cup is tilted or turned upside down.
Since the molten metal is a liquid, gravity causes it to drip in the same way. In posture welding (welding in upward, horizontal, and vertical directions), it is necessary to suppress sagging, which increases the degree of difficulty. The bead shape also changes depending on sagging, making it difficult to secure quality.
Also, the higher the welding current, the larger the size of the melt pool.
The greater the amount of molten metal, the more likely it is to drip, so attitude welding is carried out in the low current range, which naturally places significant restrictions on the welding conditions.
On the other hand, with downward welding, the welding current can be increased, making it easier to perform high-speed welding.
In this way, position welding is not impossible, but downward welding is the basic method from the viewpoint of quality assurance, ease of welding, and tolerance of conditions.