What is an industrial robot?
"Robot" is a keyword whose meaning is widely known and which has fluctuations. Various objects such as human-shaped machines and large machines that people ride and operate are associated.
The word robot was first conceived in a play by Karel Čapek in the early 20th century.
Since then, it has been depicted in numerous works, and products bearing that name have been launched into the world.
Against this background, there are a wide variety of things that are regarded as "robots" today.
"Industrial robots" are already used in many industries and support our lives.
Industrial robots are now being used in various industries, such as automobile and auto parts industries and the machinery and metal industries, in addition to the semiconductor manufacturing and logistics.
The definition of an industrial robot is a machine that takes over harsh work, heavy labor, and work that requires precise repetition in place of humans, and contributes to improving productivity in industry.
History of industrial robots
History
In the United States, the first commercial industrial robot was created in the early 1960s.
Robots were introduced to Japan in the late 1960s, which was undergoing a period of high economic growth at the time.
Then, in the 1970s, efforts toward the domestic production and practical application of robots began.
Since then, prices have risen due to the two oil shocks of 1973 and 1979, and the momentum to reduce production costs has increased, and this will permeate the industry.
The year 1980, when robots began to spread rapidly, is said to be the year when robots became popular.
The aim of using robots in the early days was to replace harsh operations in the manufacturing industry, but robots also have the advantage of continuous operation and accurate repetitive operations, so they are more widely used today for improving industrial productivity. Applicable fields are expanding not only in manufacturing processes but also in various fields, including transportation and logistics.
Our involvement
Originally, welding work was automated using submerged arc welding machines and specialized machines. In response to the need for general-purpose automatic welding equipment, we manufactured welding robots. In the late 1970s, we unveiled the first welding robot, and in 1980, we began selling general-purpose arc welding robots.
With robots becoming increasingly popular, we have developed 100% teaching operation at hand and cooperative control (synchro-motion function) among devices as early as possible. Today, we have the world's top share* in the field of robots for arc welding applications.
We have also been developing robots that can be used in a variety of applications with good operability in order to respond to the diverse challenges of our customers.
Its application is not limited to arc welding, but is spreading to various fields including material handling and mating.
*Fuji Keizai survey (FY2020 results)
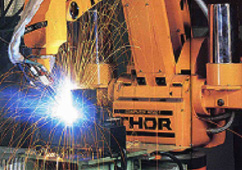
Universal Arc-Welding Robot (THOR-K)

Coordinated control (Synchro motion function)
Configuration of the robot
Industrial robots have a mechanism similar to that of the human body, as they carry work instead of people.
For example, when a person moves his/her hand, he/she moves his/her arm by transmitting commands from his/her brain through his/her nerves and moving his/her arm's muscle.
Industrial robots have a mechanism that serves as an arm and its muscles, and a controller that serves as a brain.
Mechanical section
The manipulator is a mechanical unit. Manipulators are available in various portable weights so that they can be used separately according to the work.
In addition, the manipulator has multiple joints (called joints), which are connected by links.
Control unit
The robot controller corresponds to the controller.
Based on the stored program, operation processing is performed, and based on this, commands are given to the servo motor to control the manipulator.
The robot controller is connected with a teach pendant that serves as an interface for communication with people, and an operation box equipped with buttons for starting and stopping, emergency switches, etc.
The manipulator is connected to the robot controller with a control cable that routes the power to move the manipulator and the signals from the robot controller.
The manipulator and the robot controller make the arm that remembers the movement freely and moves according to the instruction, but they also connect peripheral equipment according to the application in order to carry out specific work.
There are various end effectors (tools) depending on the work, and these tools are attached to the mechanical interface at the tip of the manipulator.
Furthermore, by combining the necessary peripheral equipment, it becomes a robot that corresponds to the desired application.
※For example, in arc welding, a welding torch is used as an end effector, and a welding power source and feeding device are used as peripheral equipment in combination with the robot.
In addition, robots may use sensors to recognize the surrounding environment.
It functions like the human eye (sight) and skin (tactile sense).
By obtaining, processing, and utilizing the information of the object from the sensor, the movement of the robot can be controlled according to the state of the object.
Robot mechanism
When manipulators of industrial robots are classified according to mechanisms, they are roughly divided into four types.
Term |
Definitions |
Cartesian robot |
The mechanical structure of the arm is mainly in Cartesian coordinate format |
Cylindrical robot |
The mechanical structure of the arm is mainly in cylindrical coordinate format |
Polar robot |
Arm mechanical structure in polar coordinate format |
Articulated robot |
The mechanical structure of the arm consists of three or more revolute joints |
1Cartesian robotics (Cartesian Robot)
The arm is driven by a translational joint, and its strength is that it has high rigidity and accuracy. On the other hand, there is a disadvantage that the operating range of the tool is narrow with respect to the ground contact area.
2Cylindrical robotics (Cylindrical Robot)
The first arm is driven by a rotary joint. Compared to a rectangular coordinate robot, the operation range is easier to secure.
3Polar robotics (Polar Robot)
The first and second arms are driven by rotary joints. The advantage of this method is that it is easier to secure the motion range compared to cylindrical coordinate robots. However, the calculation of the position becomes more complicated.
4Articulated robotics (Articulated Robot)
A robot in which all arms are driven by rotating joints.
AIts strength lies in its extremely large operating range relative to its footprint.
AAlthough the complexity of calculation was a drawback, it has become the mainstream of industrial robots due to the speedup of calculation processing due to the advancement of electronic components.
AOur specialty is this joint robot.
ABy the way, most joint-type industrial robots have six rotating axes.
AThis is because the position and orientation can be arbitrarily determined with six degrees of freedom.
AHowever, even with 6 axes, there are situations where it is difficult to take a posture depending on the shape of the workpiece. (When wraparound is required, etc.)
In order to respond to such situations, we also have a lineup of 7-axis robots.
Benefits of using robots
Using robots has the following advantages:
1High efficiency
High-speed operation without pauses is possible, which increases productivity.
2Stable quality
Stable repetitive operation reduces quality variations that can occur manually.
3To secure the labour force
This system covers the shortage of bearers due to the decreasing birthrate and aging, and it can take on long-term work with a heavy load.
4Improvement of the work environment
Robots can substitute for heavy loads or dangerous work, so people can devote their power to more specialized work.
Teaching (teaching)
In order for the robot to do work, it is necessary to program to teach and memorize the robot's movement. The task is called teaching.
There are two main teaching methods: teaching using the teach pendant and teaching using the robot directly to learn how to operate it (direct teaching).
Teaching using the teach pendant has different strengths: the robot moves by simply pressing each button, and application commands are also available at hand, while direct teaching intuitively brings the robot to the target position.
Our robots are based on the method of teaching with a teaching pendant.
In addition, we will make optimal proposals according to the environment, such as WiTP, which makes the teaching pendant wireless and easy to handle, and JoyPEN, which has a built-in gyro sensor and can be intuitively operated like a game.
In addition, today, there are also functions that reduce the effort required for teaching, such as automatically creating patterned programs by entering parameters.
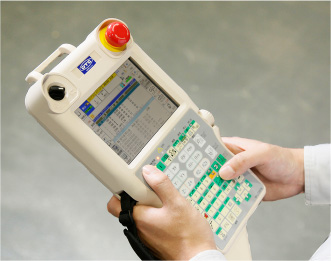
teaching pendant
Robotic automation
Industrial robots are used in many different applications, including the following.
Arc welding
This is an application triggered by our robot development. An arc, which is a discharge phenomenon, is used as a heat source to generate an arc between the object to be joined and the electrode, and the heat is used to melt and join metals.
Plasma cutting
This application concentrates the energy of the arc in the cutting area and fuses it. It is widely used in situations where metal cutting is required, such as cutting pipes and steel sheets.
Laser welding/cutting
Energy from the laser beam is used as a heat source to melt the metal, which is then joined or cut. This is used when very high-speed construction is required or when you want to suppress distortion of the object caused by the heat source.
Material handling equipment
This is an application for transporting raw materials, work-in-process and finished products within the factory.
Palletizing and depalletizing
This is an application for arranging and loading (palletizing) cargo boxes on pallets, which are mainly used in incoming and outgoing shipping processes, and unloading (depalletizing) cargo boxes from pallets on the contrary.
Sealing
This application applies sealing material to workpieces to ensure airtightness and watertightness between members.
Fitting
This application uses a force sensor to detect how a minute force is applied and automates the work of fitting. Our robot manufacturing factory uses its own robots to fit reducers.
Spraying
This is a surface treatment application that forms a coating on the work surface by heating and melting the sprayed material and spraying it onto the work.
Advantages of robot welding
The advantages of robot welding are mainly ① relieving people from severe work, ② achieving uniform work results, and ③ increasing productivity as they move at high speeds without rest.
Welding uses the heat of the arc, which is a discharge phenomenon, to melt and join metals.
Because electricity is used, improper use of this product poses a risk of electric shock or burn on molten metal.
In addition, arc light containing much ultraviolet rays and fumes, which are fine metal particles, are generated during welding. Exposure directly to these light also leads to ophthalmic and respiratory illnesses.
Therefore, when performing welding work, it is necessary to wear protective equipment such as light-resistant surfaces, dust masks, and skin gloves, as well as work clothes, working caps, and work shoes.
It is very hard to keep working on such a whole body, whether it is a cold winter day or a hot summer day.
In addition, when we work repeatedly and over for a long period of time, our people will lose their concentration of energy, and in some cases, their physical condition may not be good on some days. The body may also move reflexively or unconsciously.
In contrast, robots faithfully repeat their taught movements.
In addition, the robot is capable of high-speed welding because it can move precisely and very fast, and it stably repeats the same operation both day and night, so it is effective for raising productivity.
In recent years, we have been able to perform high-quality fabrication that is not comparable to the previous one, but because of the complexity in the structure of the tools to be fabricated, it has also emerged that it is difficult to work manually on the basis of its weight. The robots are also suitable for such advanced welding methods, as they are easily lifted, operate accurately, and do not become fatigued, even if they are heavy.
Difficulty in welding work with robots
While robotic welding has a variety of advantages, it is sometimes unfavorable for people.
In the case of welding by a person, we use skills to obtain the best welding results not only during the welding process but also before and after the welding process.
By checking how the metal is melted during welding, the speed can be adjusted, the torch position can be adjusted, and the wire protruding length can be changed. By tilting the ear to the welding sound, it can be used as an index for adjusting the quality and conditions.
Before welding, it is possible to fine-tune the conditions according to the weather by considering the change in the melting method due to the temperature difference of the workpiece, and to notice the deviation between the parts and the root gap in advance. You can decide whether to do it or rework it in advance.
After welding, you can also look at the weld and analyze its appearance.
On the other hand, the robot operates faithfully with the content taught. For this reason, it is difficult for robots to perform adjustments by human beings.
In order to solve this problem, the robot uses sensors to obtain information, which is then used to adapt the work to the actual environment.
By using the sensor, even if the arrangement of the workpiece is shifted, welding can be performed by tracing the weld line (welding point) according to the deviation, and the conditions can be changed according to the sensed route gap. In addition, the bead appearance inspection system using robots and camera sensors is becoming increasingly more stable than ever.
However, the person who teaches robot welding is very important point for stable and high-quality robot welding, since the person decides what conditions to weld under and what criteria to determine with respect to the information obtained by the sensor.
It is important that people and robots, rather than people or robots, take advantage of their respective strengths to divide their work and cooperate with each other.
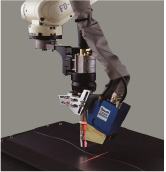
Sensor
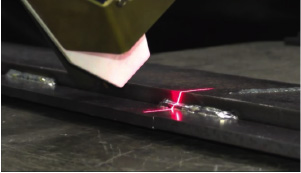
View of sensing
Qualifications required for using robots
Industrial robots are very convenient machines that can operate day and night repeatedly. However, improper use may lead to serious accidents.
For this reason, legal regulations require employees to undergo special training when they are engaged in teaching or maintenance work for industrial robots.
This special education has a curriculum in the Special Instruction Manual for Safety and Health, and both stipulate scientific and practical education.
Science will acquire basic knowledge of industrial robots and knowledge of related laws and regulations as well as their respective work.
Practical techniques are used to learn how to operate robots and how to work according to each business.
Be sure to take a course in compliance not only with laws and regulations, but also to ensure the safety of all employees.
As a comprehensive manufacturer of industrial robots, we have also prepared educational services, such as regular seminars on robot safety education courses that satisfy the requirements of special education, and we are widely supporting the introduction of industrial robots by our customers.
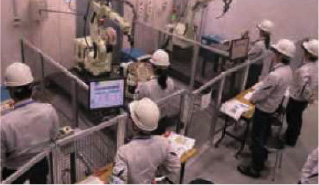
Scene of the course
Type |
Subjects |
Time |
Department |
Knowledge of industrial robots |
2 hours |
Knowledge of operations such as teaching of industrial robots |
4 hours |
Related laws and regulations |
1 hours |
Articulated robot |
How to operate an industrial robot |
1 hours |
Method of work such as teaching of industrial robots |
2 hours |
Special Education Pertaining to Service of Teaching, etc.
Purpose of using peripheral jig equipment
The peripheral jig devices are used to ensure work quality and to expand the application range of robots.
Positioner
This jig is mainly used for welding applications. In welding operations, the posture and angle of the welded portion greatly affect the welding result and its quality.
Stable welding quality can be achieved by utilizing the rotation mechanism (in the case of a 1-axis positioner) and the tilt and rotation mechanism (in the case of a 2-axis positioner) to keep the welding posture constant at all times.
Slider
The slider is a peripheral device with a linear motion mechanism equipped with a manipulator, which can expand the working range of the robot.
It is mainly used when the size of the object to be machined is larger than the operation range of the manipulator or when there are multiple machining locations and the operation range is exceeded.