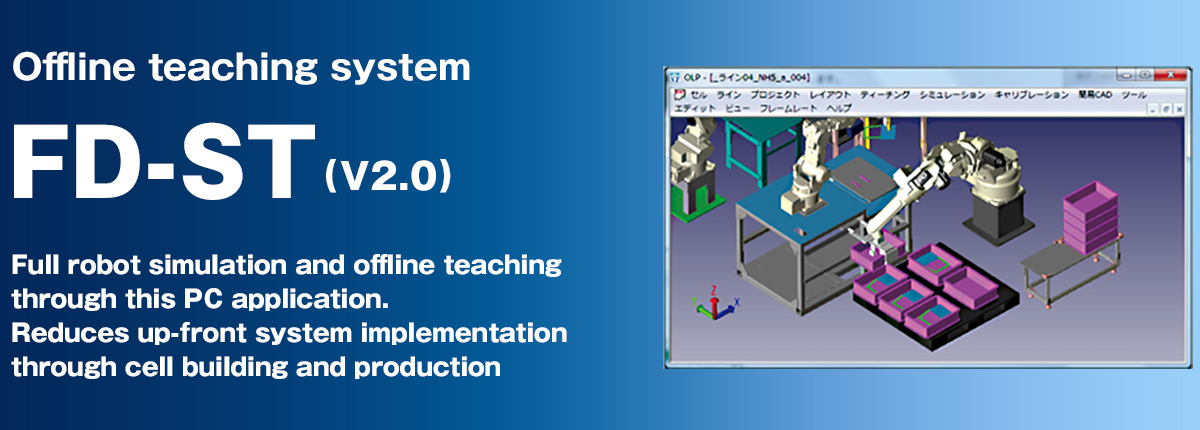
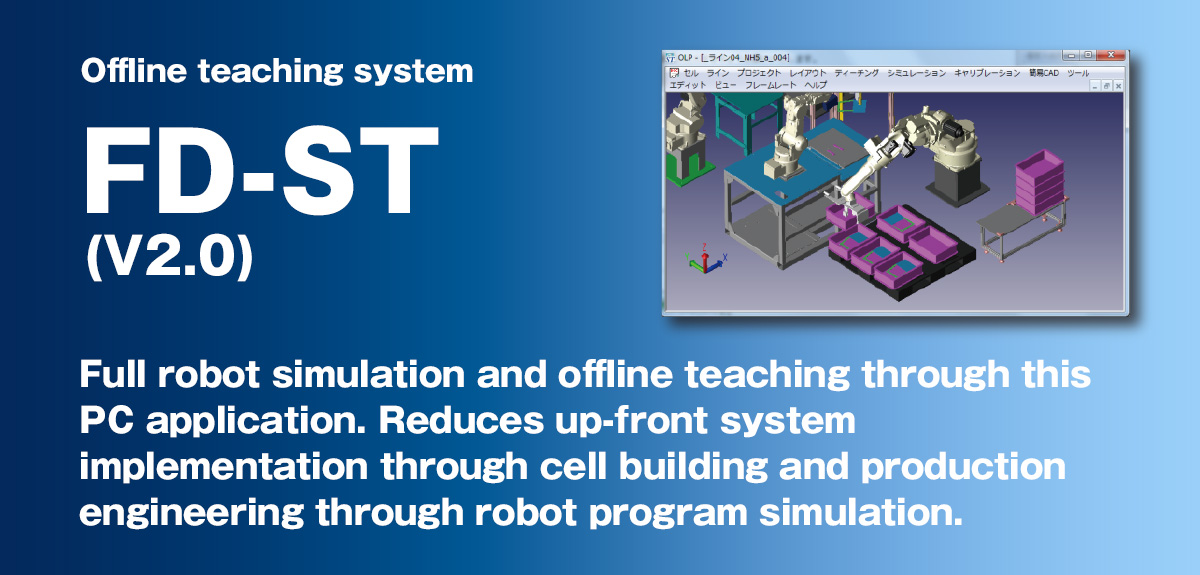
Main features
- Offline 3D cell layout, programming and simulation package.
- To ensure that teaching can be performed from multiple points-of-view, a multi-viewer, object transparency setting, measurement function and angle monitor are available.
- Simplified external axis teaching
- Automatic adjustment of the external axis of the positioner and slider for optimal welding, all at the click of a mouse.
- Sensor program can be automatically created.
- Offline and shop floor teaching time can be greatly shortened through the automatic creation of touch sensor work programs.
- Reduce the man-hours required for teaching / simulation of your production line / robot cell.
- Grouped simulation of multiple robots are available with the line layout creation function.
I/O synchronization allows linked operation of multiple robots.
- Automatic creation of work programs from your CAD data.
- Automatic creation of processing path programs from your CAD data.
Teaching has been simplified for the entire range of possible robot applications.
Specifications
Function list
Application examples | Functions |
---|
Robot introduction examination support | Automatic layout |
---|---|
Robot operation work envelope confirmation | |
Torch modeling | |
Layout data output | |
Measurement (distance measurement) | |
Offline teaching | Multiviewer |
Transparent / Wire frame / Cross-sectional display modes | |
Easy CAD (sketcher) | |
Manual operation using an operation handle | |
Snap operation | |
External axis snap operation (option) | |
Workpiece mounting (option) | |
Automatic path creation | |
Path creation & display (option) | |
Automatic sensing path creation (option) | |
Operation simulation | Reproduction running |
Cycle time measurement | |
Interference detection | |
Near miss check | |
Track display | |
Workpiece transport (option) | |
Simultaneous simulation of multiple robot controllers |
System requirements
- Elements
- Specifications
- Basic software
- Windows 7
- CPU
- Intel CoreTM i5 2.4GHz or greater
- Memory
- 4GB or greater
- Hard disk free space
- 800MB minimum
- Display resolution
- 1280 x 1024 DPI or greater
- USB port
- USB port: USB 1.1 or USB 2.0 (software license key)